Body Restructure
There are no LVV Standards covering Body Restructure, nor is there any guidance in the ‘Hobby Car Manual’.
Nobody at the LVVTA has the required attributes required for a LVV Certifier doing Body restructure.
Yet many LVV Certifications are classed as ‘Body Restructure’, such as:
1 Cab-back removal (typically used for Motor homes and Ambulances)
2 Addition of rear ramps for wheel-chair occupants
3 Stretch Limo Conversions
4 Ute Conversions
5 “Lamborghini Door” conversions
6 Roof removal (typically used for Motor homes)
7 Convertible conversions.
8 Body swaps on chassis vehicles
In my opinion, there are so many variables involved in ‘Body Reconstruction’ Certifications, that there needs to be a formal process, carried out in conjunction with the LVV Certifier.
Don’t start off by cutting and welding, before you call in the Certifier.
Step 1 Establish what type of vehicle you are starting with.
Try to establish what level of structural performance this vehicle would originally have had.
Do not leave a vehicle WEAKER than original- many older vehicles would benefit from being made stiffer or stronger- BUT-
Crash Tested cars must NOT be stiffened or strengthened in any way that could affect crash performance- The deformation characteristics under impact are critical to occupant safety.
Frame Twist test– what this shows is a boxed frame vs an open Channel frame. Heavy trucks are always Open Channel (for good reasons), and can flex, whereas lighter trucks are usually boxed. NOTE that this test demonstrates STIFFNESS, not Strength The important thing for a LVV Certifier is to recognize what he is dealing with.
I would arbitrarily divide vehicles into:-
A 1930’s style steel body on chassis (note Ford Popular was built in this style up to 1960!) Modification of such bodies is well covered in the Hobby Car Manual, the usual challenges are fitting seat-belt mountings, or burst-proof door locks to a body which was never designed with the required strength.
B Early type Unit Construction, Citroen and Vauxhall from 1930’s, most vehicles through to around 1970. Most of these are terrifyingly flimsy, and cry out for strengthening and stiffening!
Warning- Know the difference between strength and stiffness!
In some cases you will need to allow a vehicle to continue to deflect,
(I am thinking of some American ‘body on chassis semi-monocoque’ designs)
In other cases making the vehicle stiffer is the best approach. (I am thinking of a Mk 1 Zephyr Convertible I once owned, it was so limp and flexy, it cried out for more torsional stiffness and strength!)
C Early Frontal Impact cars (from around mid 1970’s), US, Australian, Swedish, some British. E.G. Ford Falcon started to become frontal impact compliant part way through the XA production, and so presumably did Holden and Valiant. Japanese cars of this period made no attempt to meet any standard, and are notoriously flimsy.
D Later Frontal Impact vehicles– MA Class from mid 90’s. These are good vehicles to work with- they tend to have good strong structures, but not too many traps such as high strength steels, bonded structures etc.
E High Performance Frontal and Side Impact vehicles, from about 2000. Many of these vehicles have unbelievably good crash performance, and are the result of lengthy development processes. The body structures tend NOT to be easily repairable after accident damage, essentially a ‘One Hit’ Product It would be a very brave LVV Certifier who would authorize any substantial modifications to such a vehicle.
Consultation with a Repair Certifier would be well worth while at this stage.
Step 2 What structure is is it proposed to remove?
Step 3 What structural effect will this removal have? (E.g. bending, torsion, door-retention, seatbelt anchorages, collision strength etc.
Step 4 How can the structural performance be strengthened to bring the vehicle structural performance back to either- the standard that it originally had, or to an increased performance?
Understand the difference between stiffness and strength, and where too much or too little of either may be detrimental
Step 5 DON’T KNOW factor.
Sometimes the right answer is “I DON’T KNOW!”
Modern high-performance structures include many hidden subtleties, of design and of metallurgy. Repair or modification of such structures is impossible, without the knowledge that only the manufacturer possesses.
If you DON’T KNOW how a structure works, or what each part is made of, you can’t justify modifying it, and claim to retain the same performance as the original.
A discussion with a good repair Certifier will often reveal
HOW MUCH YOU DIDN’T KNOW YOU DON’T KNOW!
Some basic guidelines
1 Use similar materials and joining processes
If the vehicle is pressed sheet steel, which you believe to be low or medium strength, and joined with resistance spot welds-
Then make your modifications out of similar steel, similar gauge, joined with MIG spots or fillet welds.
EXCEPTION- If you believe the parts being added are NOT STRUCTURAL (such as High-tops on Motor-homes, or ‘Wide-Body Kits’) materials such as Glass Fibre, attached with structural adhesives should be OK)
2 If the manufacturer made a vehicle similar to what you want to build- GO HAVE A DAMN GOOD LOOK AT IT
The Ford Mustang Convertibles are worth looking at, as is the Porche Targa and Convertible models.
Even a vehicle of different make, but with similar level of technology will give you an idea of what works.
3 Quality Control- Think “How do I know that this is as strong as I want it to be?”
E.G. A bolted join is very easy to check.
E.G. A Mig-welded join is also easy to check- check the strength of the MIG weld, check that material thicknesses are similar, check that the material has not changed it’s hardness (as high tensile steel could). A Mig welded joint should be as strong as the original material.
E.G. A Bonded join- is more difficult. Check carefully (if you can) that the bonding conditions met the adhesive manufacturers specifications, and that there is no surface coating which could peel off. Check also that the rated strength of the adhesive system is more than what the join requires. If you don’t know what the loading is of the joint, it may fall into the “I DON’T KNOW” category, in which case you have a problem.
4 “LAMBO DOOR HINGES” There are all sorts of kits available on the net. Most seem to be designed to be welded to the A-Pillar and to the door. I believe that this sort of attachment compromises the frontal impact and door retention standards because of the difficulty of proving otherwise. It IS POSSIBLE to build hinge systems to attach to the OEM Door Hinge mounts without any need for modification to the vehicle structure.
Some examples with pictures still to come……
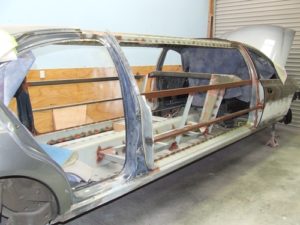
Ford Falcon Stretch Limo under construction- The inserted section carries bending and torsional loads well, and as part of the cabin is not considered to affect Frontal Impact performance
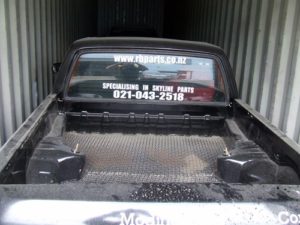
Nissan Skyline Utility-
Folded box beam joins wheel-arch and B-pillar which is butressed to replace structure removed
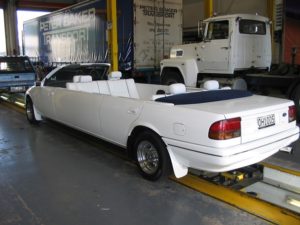
The structural strength comes from increasing the section modulus of the sill members with added material top and bottom This vehicle was subjected to rigorous beam and torsional bending tests, and is LESS FLEXIBLE than a new Saab 9.3 Convertible tested for comparison
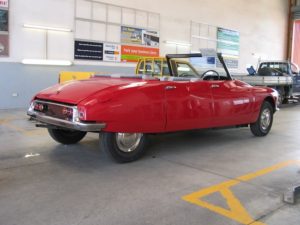
Citroen ID19 Convertible. In this case, the Citroen floor platform provides all the beam and torsional strength needed, removing the top does not weaken the car.
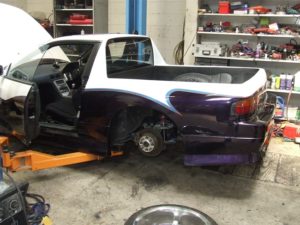
Nissan Silvia Utility. This is a frontal impact compliant vehicle with a major mod to the passenger compartment.
Most recent comments